Cleanroom validation is simply a process of filing documentary evidence that shows any procedures, testing, and productivity activity conducted within cleanrooms that testifies for a desired level of compliance. We provide a full range of ISO and EU GMP Cleanroom Testing & Validation Services. We are specialized in testing and re-qualification of cleanrooms as per ISO 14644 guidelines / EU GMP.
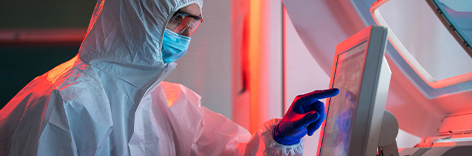
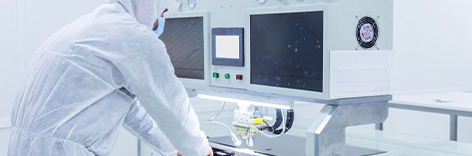
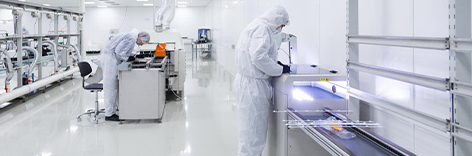
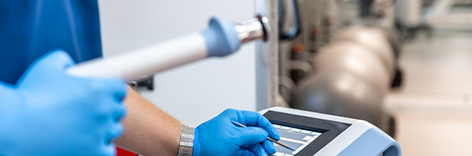
Cleanroom validation is simply a process of filing documentary evidence that shows any procedures, testing, and productivity activity conducted within cleanrooms that testifies for a desired level of compliance. We provide a full range of ISO and EU GMP Cleanroom Testing & Validation Services. We are specialized in testing and re-qualification of cleanrooms as per ISO 14644 guidelines / EU GMP.
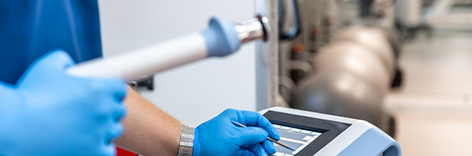
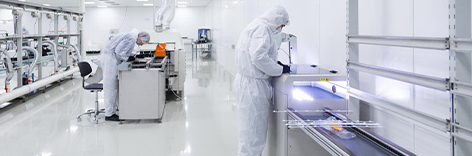
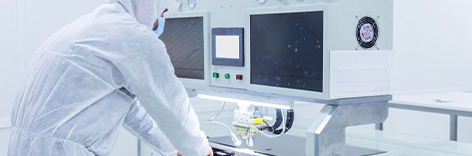
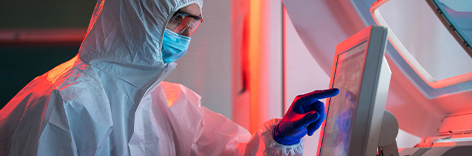
Type of Clean Room
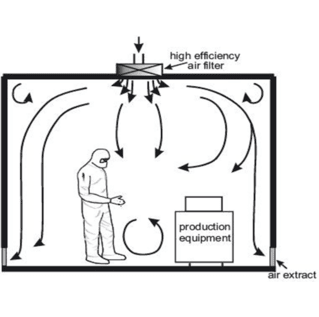
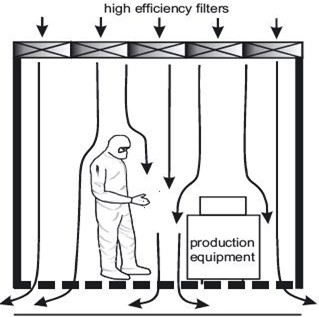
Principles of Cleanroom Testing
1. The air supplied to the cleanroom is of sufficient quantity to dilute or remove the contamination generated in the room.
2. The air supplied to the cleanroom is of quality that will not add significantly to the contamination within the room.
3. The air within the cleanroom suite moves from clean to less-clean areas to minimize the undesirable movement of contaminated air. Air should move in the correct direction through doorways and the construction fabrics of the room.
4. The air movement within the cleanroom should ensure that there are no areas within the room with high concentrations of contamination.
Cleanroom Validation Tests
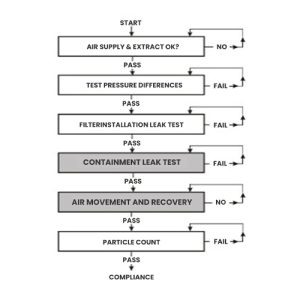
Air Supply & Extract Quantities
In the case of non-unidirectional ventilated area, the air supply should be measured. In the case of unidirectional airflow it should be the air velocity.
Pressure Differential Between Areas
It is necessary to demonstrate that the airflow between areas in the clean room suite is in the correct direction i.e. from the clean to the less-clean. This is ascertained by ensuring cleanest area is at a higher pressure than the less-clean area and the pressure differences between areas are correct.
HEPA Filter Leak Test
The high efficiency air filter, and its housing, should be checked to ensure that no airborne contamination is supplied to the cleanroom as a result of it bypassing the filter installation.
Airborne Particles & Microbial Concentrations
If the above tests are satisfactory, then measurements will be carried out to ascertain that the concentration of particles and, where appropriate, micro-organisms complies with the design specification laid down for the room.
Additional Tests
The following tests carried out the clients’ additional requirements:
1. Temperature
2. Relative Humidity
3. Sound Levels
4. Light Levels
5. AHU Visual Inspection
Testing Areas
1. Operation Theatres
2. Negative Pressure Isolation Room
3. Lab
3.1 Bio-safety Cabinets
3.2 Fume Hoods
3.3 Laminar Flow Hood
4. Clean Room
5. Ante Room
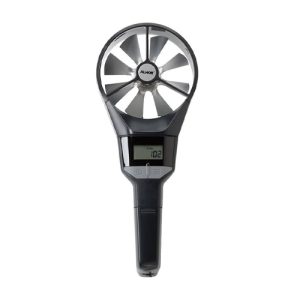
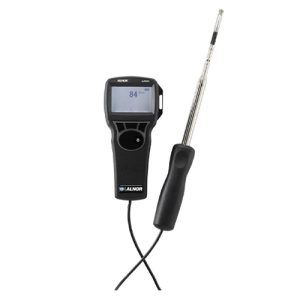
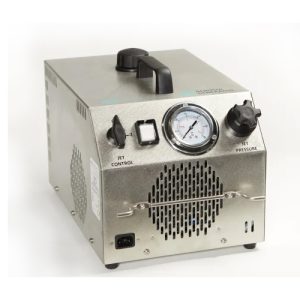
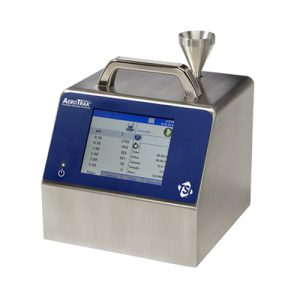
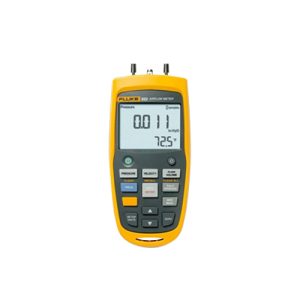
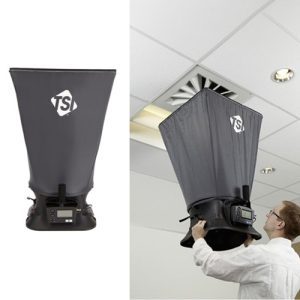
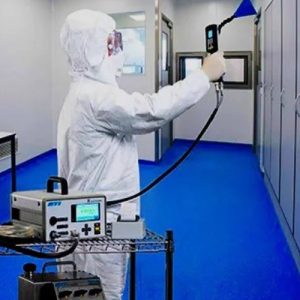
Methods for evaluation and measurements for Certification are specified in ISO14644-3. It calls out for the following ten tests.
We conduct Air Velocity Measurement / tests to determine the average filter face velocity and uniformity, and the average room airflow velocity and uniformity within a clean room. The average airflow velocity is calculated by dividing the total of the airflow grid velocities by the number of readings taken. Air Exchange Rate tests determine the total air volume get in to the room within a clean room. The use of TSI AccuBalance Air Capture Hoods of Model No.8375, assures accurate test results. The hood measures air volume flowing through registers, diffusers, and grills. Weighing just 3.5 kgs, these air capture hoods are easy to use and carry. These hoods simply hold the AccuBalance up to a diffuser or grill and read direct supply or exhaust airflow on the large digital display.
We conduct complete HEPA/ULPA filter integrity testing services. These are offered for both the Pharmaceutical and Microelectronics industries. All filter integrity tests performed by us are executed in accordance with IES-RP-CC-001-86 & ISO 14644. We are equipped to perform HEPA Filter Integrity Test with both Di-Octyl Phthalate (DOP) and Poly Alpha Olefin (PAO) depending on client-facility’s specific requirements. The tests assure that client’s filters are in conformance with various standards and/or governing agency requirements. Testing and evaluating filters minimum once annually and potentially twice annually is required for optimum performance. Proper documentation and certification is provided by us and this also helps predict potential performance issues and increases filter life.
We are Autocal a reputed name in offering clean room validation services. Our Particle Count Test provides complete airborne particle count cleanliness classification. The test is performed to determine the actual particle count level within the facility at the time of the test. The test identifies particle count on basis of As-Built, At-Rest, or Operational as per ISO 14644 , EU GMP . The particle size(s) of interest, the room occupancy state and the room classification shall be known prior to the beginning of the tests and shall be as specified in the URS documents.
We execute recovery tests for clients across Industries. These tests demonstrate the ability of the clean room to remove particulate by purging the area with filtered air. It also testifies if the room can change from a “dirty” to “clean” state within the specified time. The test is conducted by experienced technicians from the team. Our technicians have enriching experience and provide clients with high quality service. The goal of our company is to assure complete satisfaction of clients through effective execution of services and by providing the best array of clean room equipment. We ensure that the client’s clean room facility is performing properly and accurately.
Clean Room laminar flow tests
- Airflow balancing
- Fume Hoods
- Point Exhaust tests
- Personnel safety exhausts verification
- Pressure balancing between rooms and spaces
- Leak detection in ducts
We conduct Room Pressurization Test for industrial clean rooms. As a part of the validation process, this test verifies that a pressure differential meets the specified requirements.
We conduct Containment Tests for client’s clean room facility. The test is carried out to demonstrate that airborne contamination does not enter from a higher-pressure area adjacent to the clean room by means of leaks in the construction materials. The test is conducted by trained and experienced technicians using modern instruments that assure accurate results.
We conduct validation tests that include Temperature and Humidity Measurements / Tests. Two levels of temperature and humidity tests are used by us depending on the requirement. In the first level, general temperature and humidity uniformity are tested. The general level test is used to ensure that the clean room’s HVAC system maintains the specified levels of temperature and humidity required for occupant comfort. The second level or the comprehensive level test identifies that the clean room HVAC system needs to maintain the specified levels of temperature and humidity required for both occupant comfort and process temperature control.
The purpose of the lighting level tests is to verify that the installed light levels and uniformity meet the specified requirements. We make use of modern testing instruments for assessment of illuminance (lux) levels and intensity.
We perform noise level tests that measure the sound pressure. The measurements will vary based on the occupancy of a state-of-the-art clean room. The purpose may vary but the procedures of testing are identical.